
[ad_1]
A take a look at enhancing motor effectivity in two fundamental classes: electrical and mechanical.
Common readers of Charged don’t must be instructed that the standard EV drivetrain is far more environment friendly from battery to wheels than its ICE-based equal, however it’s maybe much less well-known that the approximate drivetrain effectivity ranges from 75-90% for the EV to a moderately much less spectacular 20-35% for the ICE automobile. The overwhelming majority of losses in an ICE automobile happen within the conversion of chemical power to mechanical—the so-called Carnot Effectivity—which could strategy 40% in the very best of instances. In distinction, the primary drivetrain parts in an EV—battery, inverter, motor, and equipment discount and/or transmission—all have efficiencies within the mid-to-high 90-percent vary. Nonetheless, out of these particular person drivetrain parts, many of the losses come from the motor (tied, maybe, with losses from the gear discount/transmission), therefore it’s the most promising goal for enhancing total effectivity in an EV. That stated, it’s value mentioning that enhancing the effectivity of the traction motor from, say, 94% to 97%, would require slicing losses in half. And to succeed in the identical 99% effectivity as the standard lithium-ion battery (outlined by the ratio of cost in vs. cost out, or the coulometric effectivity), would require a downright heroic discount in losses of over 83%!
Out of the primary drivetrain parts in an EV, many of the losses come from the motor (tied, maybe, with losses from the gear discount/transmission).
In gaming out the methods to enhance motor effectivity, there are two fundamental classes of losses to contemplate: electrical and mechanical. Electrical losses embody the I2R, or standard ohmic resistance, of the windings (together with the shorting bars within the rotor of an AC induction motor), the frequency-dependent modifications in these resistances on account of pores and skin and proximity results, and the assorted “iron” losses incurred within the magnetic circuit between stator and rotor, reminiscent of magnetic hysteresis—whose losses enhance with frequency—and flux leakage—whose losses are extra the results of the bodily building of the motor.
Mechanical losses embody friction within the bearings (a linear perform of RPM), displacement of grease within the bearings (a cubic[!] perform of RPM), and displacement of air (or, worse, a liquid coolant reminiscent of glycol antifreeze, oil, and many others) by the rotor meeting (aka windage, which can be a cubic perform of RPM). Frictional losses ought to be such a small a part of the whole losses in an EV traction motor as to represent a rounding error—if not, you’ll virtually actually be made conscious of the difficulty by the horrendous squealing that sad bearings inevitably produce. It’s value mentioning, nevertheless, that the largest driver of losses is, properly, the motive force—or, extra particularly, the place on the effectivity map the motor spends most of its time working (see Fig. 1).
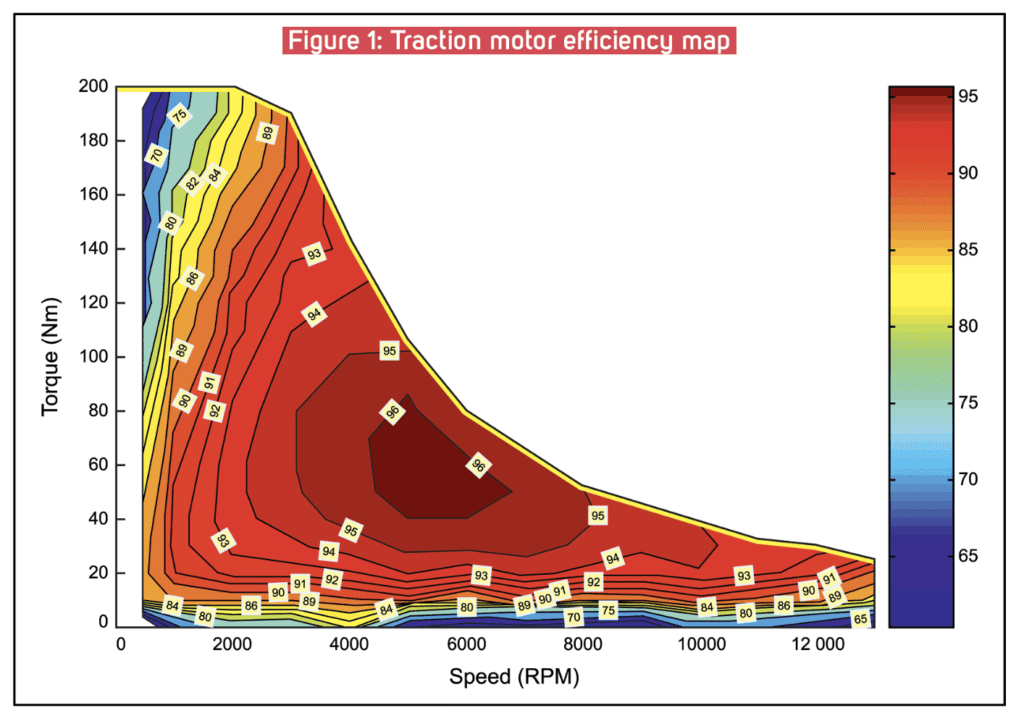
Whereas the particular effectivity values will range from motor to motor, and with software, after all, the final distribution of these values will have a tendency to use to all instances, and the important thing takeaway right here is that working on the extremes of the torque or velocity functionality of any given motor ends in drastically decrease effectivity (plummeting to zero, in reality, at max torque and 0 RPM—that’s, stalled—or any RPM and 0 torque—that’s, unloaded).
The important thing takeaway right here is that working on the extremes of the torque or velocity functionality of any given motor ends in drastically decrease effectivity.
Minimizing electrical losses requires a multi-pronged strategy, and that normally implies that there shall be some tradeoffs concerned. For instance, torque is proportional to magnetic flux depth, which itself is proportional to the product of present and the variety of turns in every armature winding, so doubling the variety of turns cuts the required present to supply the identical torque in half. This may end in a winding with twice the resistance, however since losses are proportional to present squared, the web impact is a 50% discount in losses. So why not go along with 10 occasions the turns and 1/tenth the present—or nevertheless a lot additional you need to take this argument? Effectively, the again EMF produced by a motor is proportional to the variety of turns, too, so the battery voltage essential to function at a helpful RPM would quickly exceed what’s sensible.
One other strategy is to make use of silver wire moderately than copper (or aluminum) for the windings, netting a discount in resistance of about 7% (or 39% for aluminum), albeit at a tough-to-swallow 100x enhance in value. Nonetheless, when extrapolated to a theoretical helpful working lifetime of, say, 10,000 hours, at a mean energy of 20 kW and a value per kWh of $0.20, that will save round $2,800 in electrical energy, making a reasonably compelling argument for silver windings proper there. After all, the very best winding materials can be one with no resistance in any respect—that’s, a superconductor—however the just lately damaged promise of LK-99 exhibits us that that purpose continues to be some methods off sooner or later, and even when it have been out there right this moment, there are different sensible concerns, reminiscent of whether or not the superconducting materials could be fashioned right into a wire with an enamel insulating coating, as is required for the windings in motors (and transformers, inductors and different electromagnetic parts).
Resistive losses aren’t only a drawback at excessive torque (i.e. excessive present) ranges—they will sap effectivity at excessive RPM too, because the efficient resistance of a wire quickly will increase above a sure frequency due, primarily, to the phenomenon colloquially often called “pores and skin impact.” What mainly occurs is that an alternating present induces small loops, or “eddies,” of present in its personal conductor. These eddy currents oppose the movement within the heart of the wire and add to it within the periphery, therefore it seems that the present is constrained to the outermost portion, or pores and skin, of the wire. The efficient depth that present will use in a conductor is inversely proportional to frequency, and since motor RPM is straight proportional to frequency, this units an higher restrict both on wire diameter (and due to this fact present) or RPM. The standard answer to minimizing pores and skin impact is to interrupt up a single wire into many individually insulated smaller wires—one thing which could must be performed, anyway, simply to make winding the motor (or transformer, and many others) sensible. Be aware, nevertheless, that this will increase the proportion of the winding space that’s taken up by insulation, moderately than copper (or silver, and many others), so there’s undoubtedly a legislation of diminishing returns right here.
Turning now to the iron losses in a motor, a generally used rule of thumb for any electromagnetic machine which handles alternating present is that the iron and copper losses ought to be roughly equal. As this rule of thumb implies, there are mutually unique tradeoffs between the 2—for instance, growing the cross-sectional space to cut back flux density reduces iron losses however requires longer windings, which will increase resistance (it additionally makes the motor considerably heavier). The overwhelming majority of motors right this moment use metal that’s alloyed with silicon to assemble the magnetic circuit—that’s, the elements of the motor that conduct loops of magnetic area—because it combines a comparatively excessive saturation flux density, good formability, excessive electrical resistance, and comparatively low value, however on the expense of less-than-impressive hysteresis losses (roughly equal to frequency-dependent losses in wires). Worse nonetheless is that the losses in a magnetic materials have a tendency to extend at an exponential price with frequency and flux swing (usually to the 1.5-2.5 energy, relying on materials), which means {that a} comparatively small enhance in inverter elementary frequency (which determines RPM) or section present (which determines torque) can lead to an outsized enhance in losses.
There are quite a few magnetic supplies with a lot decrease losses, however few of them are appropriate to be used in motors. For instance, the assorted ferrites generally utilized in high-frequency magnetic parts have a decrease saturation flux density (within the vary of 0.3-0.35 Tesla, in comparison with 1.8-2.0 Tesla for silicon metal) and are extraordinarily brittle, in order that they’re tough to type, and aren’t the only option for a motor that shall be bouncing alongside the highway. Far more promising supplies make use of slight variations within the processing and/or alloying parts of silicon metal, leading to both a particularly fantastic grain construction (nanocrystalline) or no grain construction in any respect (amorphous). Amorphous metals have been employed in transformers and motors for many years (and for these of a sure age, additionally within the heads in tape decks) and whereas they will obtain a formidable as much as 70% discount in losses (from round 1.4 W/kg to 0.4 W/kg, relying on frequency, flux swing, and many others), they’re dearer to fabricate and extra brittle (although not almost as brittle as ferrite). Between the 2 variants, the nanocrystalline model has the sting in saturation flux density and mechanical properties, whereas amorphous is inexpensive to supply and a extra established materials. Both approach, decreasing iron losses by as much as 70% will get you nearer to enhancing total motor effectivity to that legendary 99% determine than the comparatively meager contribution from silver wire, and probably at a decrease value.
Decreasing iron losses by as much as 70% will get you nearer to enhancing total motor effectivity to that legendary 99% determine than the comparatively meager contribution from silver wire, and probably at a decrease value.
As talked about earlier, frictional losses within the shaft bearings ought to be a tiny fraction of total losses, so this isn’t actually an space the place additional optimization is feasible, though we should always word that one insidious failure mode of motors equipped by a variable-frequency drive is spark erosion of the interior bearing surfaces brought on by capacitively-coupled currents produced by the quickly switching voltages from the inverter (i.e. from excessive dV/dt), therefore the rising use of ceramics for the bearing balls and races. In any other case, transferring away from total-immersion liquid cooling—particularly if the coolant is oil, which has a a lot increased viscosity than aqueous coolants like glycol and water—can considerably scale back windage loss. One other key issue just isn’t working at extraordinarily excessive RPMs, as, once more, windage loss scales with the dice of RPM, so a modest lack of 100 W at, say, 3,000 RPM turns right into a far-less-tolerable 2.7 kW of loss at 9,000 RPM.
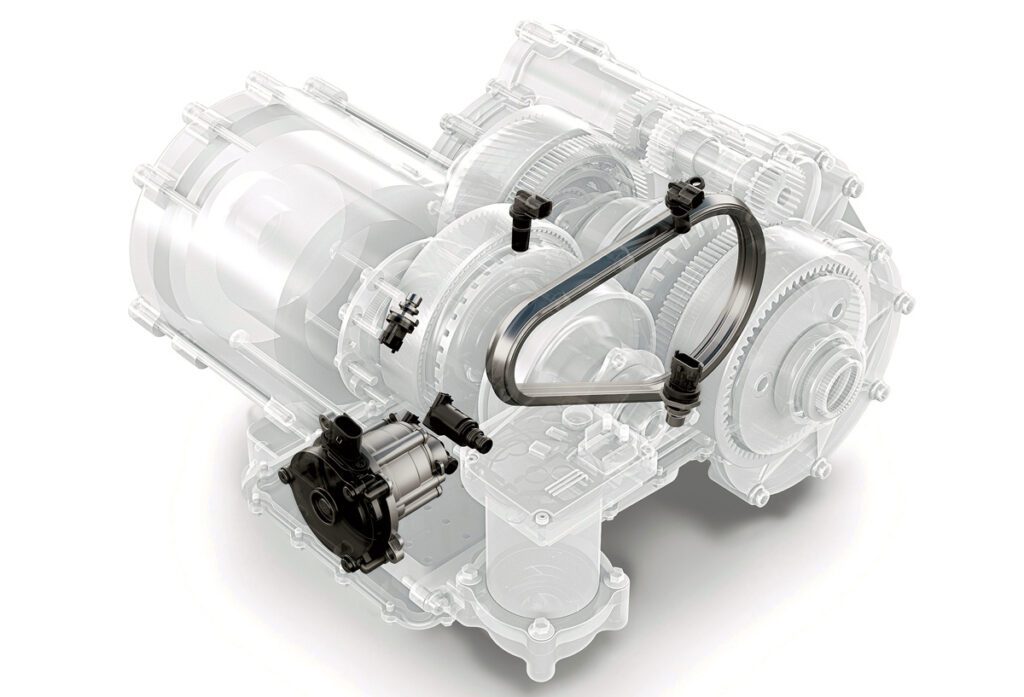
Image: Bosch
On a associated word, the usage of multi-speed transmissions (both mechanical or the moderately novel digital strategy mentioned beneath) moderately than the single-speed gear discount mostly utilized in EVs right this moment may also help hold the traction motor in that candy spot of average torque and average RPM for a better proportion of time (whereas enhancing acceleration and prime velocity). With a mechanical transmission there shall be some enhance in frictional/windage losses (notably for gears bathed in oil), however the typical 97-98% effectivity of a gear practice will at all times examine favorably to working within the sub-70% area of the motor’s effectivity map. For instance, each Porsche and Audi have used a two-speed gear transmission of their EVs, however Bosch is at present making the case for its CVT4EV, which is a constant-velocity transmission that’s optimized for EVs by slicing its velocity discount vary in half to double its most torque functionality (as in comparison with its ICE counterpart).
Alternatively, it’s doable to simulate a multi-speed transmission electronically by breaking apart the section winding pairs into a number of units that may be rewired on the fly by the inverter to alter both the obvious variety of poles or the variety of phases. Every of those options successfully modifications the rotational angle that the magnetic area produced by the stator has to behave upon—appearing over a shorter arc trades the next torque for a decrease synchronous velocity and vice versa—however a caveat is that this might require very completely different inverter {hardware} and software program, so don’t count on to see these options carried out in an OEM EV anytime quickly. That stated, historical past exhibits that each time a mechanical answer could be changed by an digital one, it’s all however positive to be adopted…ultimately.
Learn extra EV Tech Defined articles.
This text appeared in Situation 65: July-September 2023 – Subscribe now.
[ad_2]