
[ad_1]
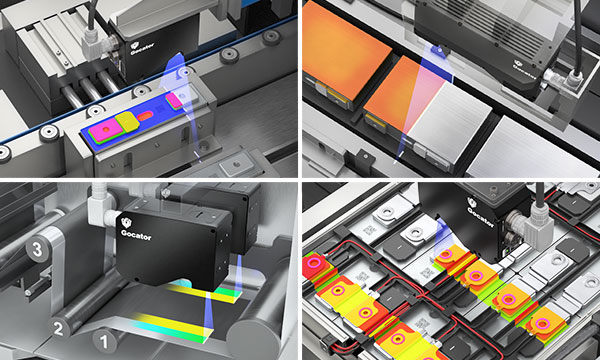
Sponsored by LMI.
The rise in demand for EV Batteries has already completely remodeled the automotive manufacturing panorama, with nearly all main automotive corporations now working electrical car manufacturing traces.
Whereas electrical automobiles do have much less shifting elements than their inside combustion engine (ICE) counterparts, manufacturing them remains to be extraordinarily complicated. From stators and rotors, to intricate wiring harnesses, LMI is concerned with many EV manufacturing functions. However the coronary heart of an EV is its battery, and that is the place machine imaginative and prescient options have turn into important to market success.
EV Battery Manufacturing Overview
EV battery manufacturing will be damaged up into 5 normal steps: (1) electrode manufacturing, (2) cell meeting and packaging, (3) cell-to-module meeting, (4) module-to-pack meeting, and (5) remaining set up inspection.
Gocator 3D good sensors and their in-built, onboard measurement instruments are utilized in each stage of this manufacturing course of.
Let’s take a look at these functions individually.
Electrode Manufacturing
Electrode slurry is coated onto copper and aluminum foil to facilitate electrical circulate. The metallic floor, separator, and coating should be inspected for edge defects in addition to uniform form and thickness.
Throughout this step, Gocator sensors are used to make sure uniform form and thickness of the electrode because the slurry is utilized. Sensors are additionally used to measure the gap between tabs on a cell sheet. Tolerances are extraordinarily small for these functions so excessive decision and small area of view sensors are used.
Sensible 3D sensors are used for various duties at this section of inspection together with:
- Electrode Width Gauging – Correct width gauging of the size of the separator and electrode.
- Electrode Edge Profile Measurement – Excessive-speed profiling of the sides of coated electrode sheets to make sure the right dimensional tolerances are met.
- Tab Distance Gauging – Scanning and measurement of the gap between tabs on a cell sheet to fulfill dimensional tolerances.
Cell Meeting and Packaging
A separator and electrode are joined collectively, and the joined cell (together with anode and cathode) is both wound, rolled, or stacked. Stacked cells are then housed in a metallic casing and sealed by welding.
Two of the most typical cell varieties utilized in electrical automobiles are cylindrical and prismatic. Cylindrical cells are packed collectively into teams and scanned for presence/absence, appropriate place and dimensions, as in addition to for potential floor defects akin to any dents or scratches on the cell prime. Solely 3D supplies the form (peak) information required to examine battery floor options and dimensions for defects akin to bulges, fissures, warps, and extra.
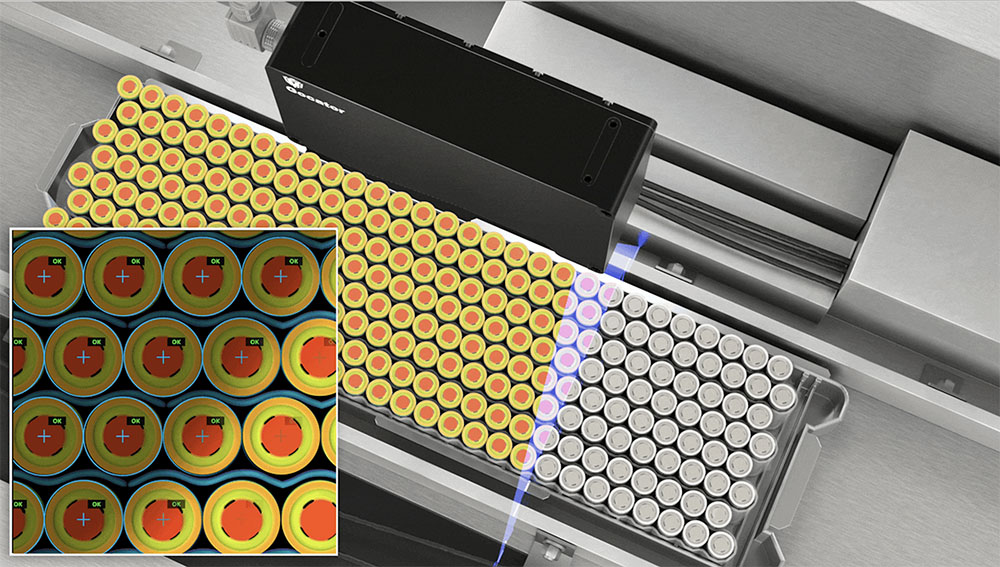
Previous to welding, a Gocator® or multisensor community delivers high-speed 3D laser profiling and a built-in device to measure the hole & flush between the prismatic battery cell and its metallic casing. After welding, they’re inspected once more to make sure that the weld seam is uniform and inside tolerances.
The floor of the battery cell must be inspected for proper dimensions and to detect defects of the face, edges, and corners. It is usually value noting that good 3D sensors like Gocator include blue laser mannequin choices. The shorter-wavelength blue gentle generates higher-quality scan information (i.e., much less noisy) on extremely specular battery surfaces akin to polished metallic.
Cell-to-Module Meeting
As soon as the person battery cells are inspected for high quality management, a set variety of them are exactly grouped collectively to type a battery module. An instance utility for module inspection is for sensors to measure and examine the weld seams of every module.
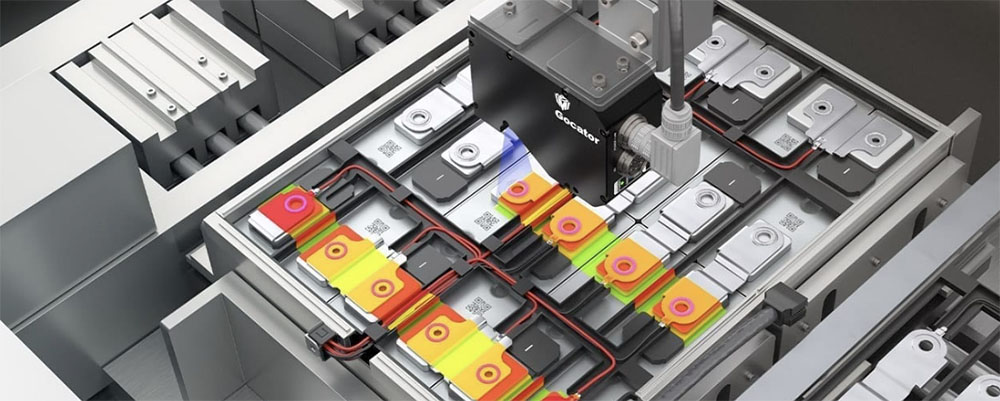
Module-to-Pack Meeting
Modules are then mixed to type battery packs. Gocator sensors are used on the remaining stage of the method, combining modules right into a single battery pack, able to be put in into a brand new electrical car. It’s essential to measure and examine its size, width, peak, and flatness of every floor to make sure that all dimensions are matching the GD&T design tolerances.
Ultimate Set up Inspection
In electrical automobiles, a big tray/pan sits beneath the ground panel. The lithium-ion battery pack is glued to this tray. Gocator sensors are used at this remaining stage to examine the glue bead utility for proper dimensions (peak, quantity, width, size) and floor high quality (breaks, gaps, overflow and so forth.).
Selecting the Proper 3D Sensor for Your EV Battery Utility
LMI Applied sciences provides a spread of laser profile sensors that may deal with any EV battery inspection utility. For instance, the Gocator 2500 Collection provides extremely high-speed blue laser profiling for high-performance inspection of shiny EV battery surfaces. Or when even larger measurement precision is required, engineers can deploy the Gocator 2600 Collection of their manufacturing traces for highly effective extremely high-resolution 4K+ profiling.
Mix Sensible 3D Scanning with AI-Primarily based Inspection
Along with its suite of high-speed, high-resolution 3D good sensors for EV battery scanning (with internet browser interface and onboard software program), LMI Applied sciences additionally supplies inspection engineers with the choice so as to add highly effective FactorySmart AI-based inspection to their EV Battery manufacturing traces for probably the most full end-to-end answer in the marketplace in the present day.
For instance, in EV battery array inspection, engineers can deploy a set of tightly built-in LMI merchandise from sensor {hardware} to edge units and human-machine interface (HMI) as a way to remedy the applying with most efficiency and cost-efficiency.
An instance of this answer would possibly embody:
- 2x Gocator 2600 laser profilers for 4K+ high-resolution 3D level cloud era of the EV battery array
- 2x GoMax NX edge units for sensor acceleration and highly effective AI-based floor defect detection
- GoFactory interface for information administration (efficiency monitoring, telemetry dashboarding, configurable alerts)
Conclusion
EV battery manufacturing continues to develop quickly world wide. LMI will not be solely supporting the present trade, however actively growing subsequent era sensors particularly designed to fulfill future battery manufacturing wants.
For extra info go to our EV Battery Business internet web page.
[ad_2]